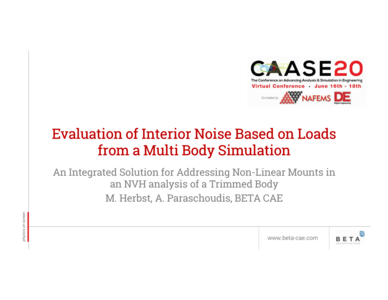
NAFEMS Americas and Digital Engineering (DE) teamed up (once again) to present CAASE, the (now Virtual) Conference on Advancing Analysis & Simulation in Engineering, on June 16-18, 2020!
CAASE20 brought together the leading visionaries, developers, and practitioners of CAE-related technologies in an open forum, unlike any other, to share experiences, discuss relevant trends, discover common themes, and explore future issues, including:
-What is the future for engineering analysis and simulation?
-Where will it lead us in the next decade?
-How can designers and engineers realize its full potential?
What are the business, technological, and human enablers that will take past successful developments to new levels in the next ten years?
Resource AbstractThe NVH performance of a car has always been one of the key factors affecting customer satisfaction as unwanted noise in the passenger cabin leads to an uncomfortable driving environment. As a result, a lot of research and testing is invested in NVH related topics.
Classical CAE NVH analysis procedures are based on linear numerical methods and linear FE models. However, it is well known that important components of a vehicle, e.g. the chassis mounts, show a strong non-linear behavior which is not captured in a linear analysis. In order to overcome this shortcoming a 2-step approach is used:
1. A Multibody Simulation (MBS) is performed which simulates a certain driving maneuver of the full vehicle. The MBS is a non-linear method and can capture non-linear characteristics via non-linear material properties, e.g. the stiffness of chassis mounts, via contacts or via kinematic constraints. The trimmed body (TB) is included in the MBS as a flexible body represented by its Modal Neutral File (MNF) modes.
2. One outcome of the non-linear MBS is the knowledge of the forces that are acting on the trimmed body at the chassis to body interface points. Assuming that the car body itself behaves linear, classical linear NVH analyses can be performed using the forces from MBS. Typical examples are the calculation of sound pressure level (SPL) or of the tactile response at locations like the steering wheel, in time as well as in frequency regime.
In this presentation a new method is introduced which reduces the files sizes of the MNF file in the same significant way as the modal base for the NVH calculation. A display model is used in both steps which is a simplified FE model consisting of a coarse shell mesh. Whereas the nodes of the display model must be a subset of the original FE, the course shell elements are just used for displaying results. Using such a display model for the MNF calculation is new feature of the BETA FEM solver EPILYSIS and a key enabler for an efficient coupled MBS-NVH process.
Furthermore, the presented analysis proves a huge influence of including the TB as a flexible component instead of a rigid body in the MBS. It is shown that a flexible body representation overestimates the forces on the TB and leads to exaggerated tactile and acoustic responses. A detailed modal participation analysis reveals that the overestimation is especially pronounced at the global modes of the TB.
Additionally, the proposed process was slightly changed. Instead of applying the interface forces acting on the body system the modal coordinates of the flexible body calculated in the MBS are used to determine the NVH Trimmed Body response. Results for both approaches are compared.