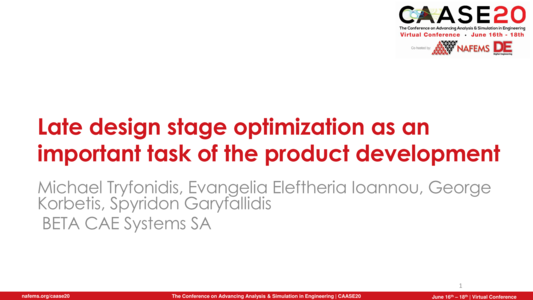
NAFEMS Americas and Digital Engineering (DE) teamed up (once again) to present CAASE, the (now Virtual) Conference on Advancing Analysis & Simulation in Engineering, on June 16-18, 2020!
CAASE20 brought together the leading visionaries, developers, and practitioners of CAE-related technologies in an open forum, unlike any other, to share experiences, discuss relevant trends, discover common themes, and explore future issues, including:
-What is the future for engineering analysis and simulation?
-Where will it lead us in the next decade?
-How can designers and engineers realize its full potential?
What are the business, technological, and human enablers that will take past successful developments to new levels in the next ten years?
Resource AbstractDuring product development, many analyses including optimization, take place at different stages of the product design. Although optimization at early stages is a very important task, as it provides solid directions for the final design, late stage optimization has significant presence in product development. Late stage optimization can act as models’ fine tuning and as a process that can fix deficiencies without the need to go back in a previous design stage. The aforementioned ability is even more valuable when manufacturing methods have been decided, acting as important constraints to the design change flexibility.
This paper investigates the case in which the performance of a BiW model must be improved at a latest stage of the design process. The aim of the optimization is to reduce the intrusion of the door and B-pillar during a side impact analysis to avoid passenger’s injury. However, special considerations and constraints such as, the constraint of the stumping and punching manufacturing processes must be taken into consideration. The success of this process depends on the minimum number of design changes. Therefore the design changes that are used could be the definition and parameterization of small features like holes, beads, etc. Additionally, small parts can be added as reinforcements in weak areas of the model. The dimensions of these parts are also taken into account as parameters of the optimization process. Finally, all actions that are considered to act as design changes (feature definition, feature modification, parts creation) should be applied on an FE representation of the BiW since the model geometry could be possibly obsolete at the latest design stage.
In this paper, an example of a BiW model subjected in side impact test will be demonstrated. The optimization process will start with a Design of Experiments run which will evaluate the most important input variables of the optimization problem. In a second step, an optimization algorithm will drive a pre- processor, solver, post- processor sequence, finding the optimum design.