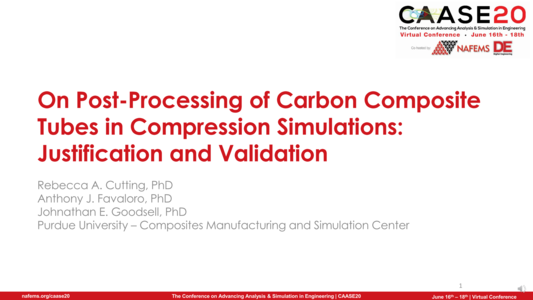
NAFEMS Americas and Digital Engineering (DE) teamed up (once again) to present CAASE, the (now Virtual) Conference on Advancing Analysis & Simulation in Engineering, on June 16-18, 2020!
CAASE20 brought together the leading visionaries, developers, and practitioners of CAE-related technologies in an open forum, unlike any other, to share experiences, discuss relevant trends, discover common themes, and explore future issues, including:
-What is the future for engineering analysis and simulation?
-Where will it lead us in the next decade?
-How can designers and engineers realize its full potential?
What are the business, technological, and human enablers that will take past successful developments to new levels in the next ten years?
Resource AbstractFinite element modeling of carbon composites materials in axial compression uses element deletion to simulate material failure. During progressive failure of geometries with a single loading surface, rows of elements can be deleted simultaneously causing the compressive load on the structure to be released, initiating a traveling stress wave. The release of the compressive load causes the reaction force at the loading surface to immediately vanish, and the resulting time history of the reaction force has a saw-tooth shape corresponding to element deletion and subsequent geometry reloading. The saw-tooth loading history is not representative of the physical reality that occurs during experimentation of such materials and geometries. Researchers have taken several approaches to deal with this phenomena when modeling, including filtering the results, incorporating new contact definitions, and altering material properties to get simulation results to match experiment.
This work proposes a new method for post-processing axial compression results of carbon composites that uses characterized material properties and addresses the cause of the irregular oscillatory behavior. In a continuous system for progressive failure, the impacting wall maintains contact during the failure process. The saw-tooth shape of the reaction force seen in finite element analysis is solely a function of discretization within the model. As the size of the elements decrease, the gap between peaks reduces linearly. Ideally, as the element size goes to zero, the saw-tooth curve disappears and provides a continuous curve. One-dimensional and two-dimensional compression models are introduced to show the effect element discretization has on the behavior of the load history for simplified geometric representations. The post-processing method of connecting the peaks of the saw-tooth reaction force curve is then justified. The post-processing method is implemented into a hollow tube model with characterized material properties and compared to experimental results without model calibration. Finally, the limitations of the method and its usefulness in complex geometries are discussed.