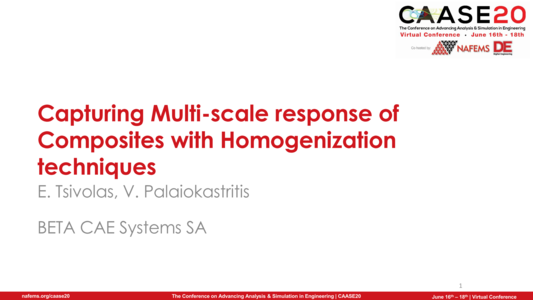
NAFEMS Americas and Digital Engineering (DE) teamed up (once again) to present CAASE, the (now Virtual) Conference on Advancing Analysis & Simulation in Engineering, on June 16-18, 2020!
CAASE20 brought together the leading visionaries, developers, and practitioners of CAE-related technologies in an open forum, unlike any other, to share experiences, discuss relevant trends, discover common themes, and explore future issues, including:
-What is the future for engineering analysis and simulation?
-Where will it lead us in the next decade?
-How can designers and engineers realize its full potential?
What are the business, technological, and human enablers that will take past successful developments to new levels in the next ten years?
Resource AbstractComposite materials have entered to the era of their extensive use as load bearing materials leading one step further the design of high performance structures. CAE solutions can offer to the engineer key tools for optimal and efficient design of composite materials that meet the engineering performance requirements. The scope of this work is to present a workflow for the Multi-scale modelling of components made with composite materials in the multi-disciplinary environment of ANSA pre-processor.
The aim of the examined case study was to substitute the metallic (aluminium) material of a beam, subjected into three-points bending, with a multi phase composite material to reduce its weight.
With known properties of the constituents, a material with equivalent response was estimated for both the linear and non linear regions, using Mean Field Homogenization formulations. The fiber orientation from the molding simulation was mapped in the structural model. Both models (metallic and composite) ran in the nonlinear regime resulting in similar flexural behavior. At the post processing level results at multiple scales can be previewed.
Furthermore, the high strain area of the model was isolated and a FE-model for the RVE was generated on given microstructure information and orientation tensor from the molding analysis. The RVE model was subjected into the boundary conditions (strain) of the macro-scale analysis to examine cases of fiber-matrix interfacial damage.
The beam made by the Composite Material had approximately half of the weight of the aluminum beam. Although in case of the aluminum and composite beam the material response did not exceed the plastic region, in microscale level fiber matrix debonding was observed at the end of the analysis.
In this presentation, the described workflow attempts to bridge the gap between Multi-scale modeling, Manufacturing Simulation and Structural Analysis, to facilitate the composite material design process.