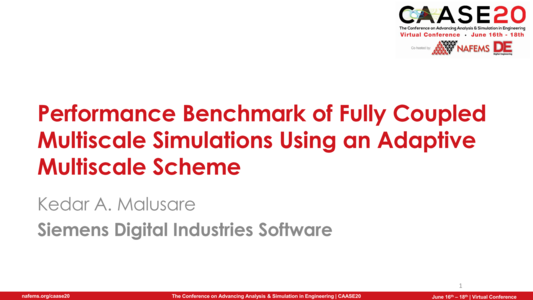
NAFEMS Americas and Digital Engineering (DE) teamed up (once again) to present CAASE, the (now Virtual) Conference on Advancing Analysis & Simulation in Engineering, on June 16-18, 2020!
CAASE20 brought together the leading visionaries, developers, and practitioners of CAE-related technologies in an open forum, unlike any other, to share experiences, discuss relevant trends, discover common themes, and explore future issues, including:
-What is the future for engineering analysis and simulation?
-Where will it lead us in the next decade?
-How can designers and engineers realize its full potential?
What are the business, technological, and human enablers that will take past successful developments to new levels in the next ten years?
Resource AbstractThe adoption of composite materials is growing rapidly to enhance structural performance across many engineering applications. However, failure and damage prediction of these advanced materials through finite element analysis (FEA) is often inaccurate and can be computationally expensive. This inaccuracy is due to the use of generalized orthotopic failure models that are based off simple uniaxial experimental tests. These material models result in long run times and high memory usage since non-linear FEA models require refined time steps and constant updating of the constitutive stiffness tensor. Through multiscale modeling, these materials can be represented more realistically and accurately since every integration point of a global finite element model (FEM) is mapped to a unique microstructural FEM. However, with this increase in accuracy comes an increase in run time and memory, due to the added degrees of freedom from the microstructural FEMs. To make this type of analysis competitive with traditional methods, an novel adaptive multiscale scheme was used to reduce the computational cost of these simulations. In this study the efficiency of this type of multiscale analysis is compared against single scale composite analysis. The global model is a 3D model of a simply supported beam. For the single scale analysis, both linear and non-linear (continuum damage) material models were used. For the multiscale analysis, four different types of microstructural models with varying mesh refinements were used: hex-pack unidirectional fiber reinforced polymer, random-pack unidirectional fiber reinforced polymer, plain weave fiber reinforced polymer, and satin weave reinforced polymer. For each global and local model, the number of elements and integrations points were documented to gauge the total number of degrees of freedom for the multiscale model. The run time and data compression efficiency for each simulation was documented and compared against the single scale simulations. The single scale simulations were unsurprisingly quicker by a factor of only 3x. As the size of the local scale model increased, so did the total run time of the multiscale model. Although the single scale simulations were still faster than the multiscale simulations, this increase in run time still allows for this type of analysis to remain feasible for commercial engineering applications, especially when considering the increase in accuracy and information received on the material’s microstructure.