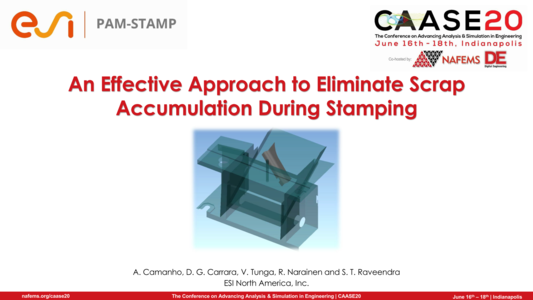
NAFEMS Americas and Digital Engineering (DE) teamed up (once again) to present CAASE, the (now Virtual) Conference on Advancing Analysis & Simulation in Engineering, on June 16-18, 2020!
CAASE20 brought together the leading visionaries, developers, and practitioners of CAE-related technologies in an open forum, unlike any other, to share experiences, discuss relevant trends, discover common themes, and explore future issues, including:
-What is the future for engineering analysis and simulation?
-Where will it lead us in the next decade?
-How can designers and engineers realize its full potential?
What are the business, technological, and human enablers that will take past successful developments to new levels in the next ten years?
Resource AbstractAn important issue in metal stamping manufacturing is the successful shedding of scrap from trim dies. Because scrap is not the primary product, it receives less attention than the finished products. However, not evacuating scrap from the die in an efficient manner causes production delays due to shut down, reduces die efficiency, and increases cost of stamping production. Thus, it is critical to establish trim die design integrity as early as possible in the design process to eliminate scrap shedding related shutdown of the press line of production. An efficient simulation/optimization process is proposed to identify the critical design parameters to eliminate scrap shedding related shutdown and inefficiencies, thus improving the manufacturing, product quality and lifetime of the trimming dies at reduced capital and operating costs.
Simulation of sheet metal forming is becoming increasingly popular and has become essential in the automotive industry for sheet metal product design, die design developments, and production stamping. Simulation shortens lead times since it can be used to reduce development cost while assessing the feasibility of part geometry. A typical stamping simulation process for a single sampling point (design variable) involves the design of die, creation of die, tryout of die, validation of die, and completion of die.
The aim of the optimization is to determine the variables that cause the accumulation and subsequent jamming of scraps in the metal stamping process. Parameters such as die velocity and type of trim operations affect the metal shedding. Since these parameters influence the forming and trimming operations, scrap shedding investigation requires the simulation of the entire, computationally expensive process. Additional parameters such as contact surface area, distance between gravity center and geometric center, shape complexity, weight and angle of inclined plane, change of friction due to accumulation of metal dust, and design of scrap chutes also affect the scrap-related inefficiency.