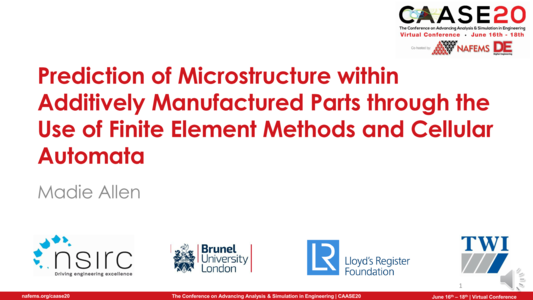
NAFEMS Americas and Digital Engineering (DE) teamed up (once again) to present CAASE, the (now Virtual) Conference on Advancing Analysis & Simulation in Engineering, on June 16-18, 2020!
CAASE20 brought together the leading visionaries, developers, and practitioners of CAE-related technologies in an open forum, unlike any other, to share experiences, discuss relevant trends, discover common themes, and explore future issues, including:
-What is the future for engineering analysis and simulation?
-Where will it lead us in the next decade?
-How can designers and engineers realize its full potential?
What are the business, technological, and human enablers that will take past successful developments to new levels in the next ten years?
Resource AbstractAdditive manufacturing (AM) is an innovative manufacturing method hailed for its ability to produce complex, topology optimised parts with high material usage. However, the wide spread implementation of this process is hindered by the lack of reliability and certification of AM parts. In particular, the microstructure of additive manufactured parts varies considerably to that of the same part made, with the same material, by traditional methods such as casting. This is due to the complex thermal history experienced by the material within the additive procedure. Changes in microstructure result in different material properties in the built part, to that of their traditional counterparts, and therefore introduce uncertainty surrounding the performance of the final product. In order to accelerate the adoption of AM within industry, through increased reliability and certification, we must first be able to understand the links between process parameters, microstructure and resultant properties through the use of integrated computational materials engineering (ICME).
Within this work a multi-scale model is implemented to facilitate the prediction of grain morphology within additively manufactured metal parts. A weak coupling is used between a thermal finite element (FE) model and a cellular automata (CA) model for solidification. Although thermal simulations of AM processes are usually used for residual strain and distortion predictions, they are used within this work to determine undercooling; the driving force behind solidification. CA works by applying a number of variables to a grid of cells. The variables are then updated according to a set of rules. In this scenario, these rules are representative of the physical nucleation and growth mechanisms. Probabilistic nucleation methods are implemented based on Gaussian distribution and grain growth and capture is determined through the assignment of a grain envelope representative of the crystal shape. This allows for the direct determination of effect of process parameters on microstructural features such as grain size and shape.
The modelling approach has been validated through a case study using single laser scans on an IN625 substrate. Open source experimental data was used, from the NIST AM benchmark 2018, to verify the microstructure predictions both visually and qualitatively. The model has since been applied to powder bed fusion and wire-arc additive manufacturing methods, whereby additional features have been added to the CA algorithm to account for the deposition of new material, in powder or liquid form. Within these models, the development of functionally graded materials through process parameter variation has been simulated and compared against experimental results in literature. Furthermore, an attempt to predict columnar to equiaxed transitions based on solidification parameters has been undertaken. The ultimate goal of this work is to contribute towards an extensive modelling method that allows for process optimisation and design for metal AM parts, enabling microstructure tailoring and control.
This work was made possible by the sponsorship and support of Lloyd’s Register Foundation and was enabled through, and undertaken at, the National Structural Integrity Research Centre (NSIRC). NSIRC is a postgraduate engineering facility for industry-led research into structural integrity established and managed by TWI through a network of both national and international Universities. Lloyd’s Register Foundation helps to protect life and property by supporting engineering-related education, public engagement and the application of research.