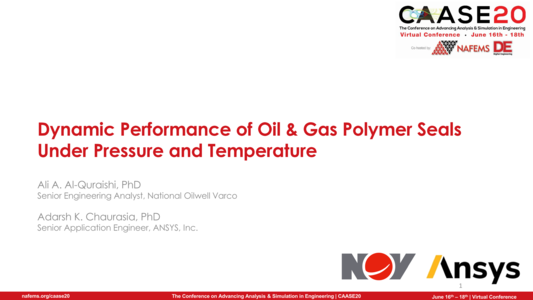
NAFEMS Americas and Digital Engineering (DE) teamed up (once again) to present CAASE, the (now Virtual) Conference on Advancing Analysis & Simulation in Engineering, on June 16-18, 2020!
CAASE20 brought together the leading visionaries, developers, and practitioners of CAE-related technologies in an open forum, unlike any other, to share experiences, discuss relevant trends, discover common themes, and explore future issues, including:
-What is the future for engineering analysis and simulation?
-Where will it lead us in the next decade?
-How can designers and engineers realize its full potential?
What are the business, technological, and human enablers that will take past successful developments to new levels in the next ten years?
Resource AbstractElastomer seals are used extensively across various industries for sealing pressures across structural interfaces. In Oil and Gas (O&G) industry, elastomer seals serve a critical function of pressure control which is critical for both human and environmental safety. Over the years, significant analysis has been performed on the behavior of these seals using finite elements. The seals undergo finite deformations (sometimes folding on themselves), have highly nonlinear contact behavior and are modeled using hyperelastic material models. In addition, these seals are subjected to very high temperatures and pressures for O&G applications which makes these problems challenging to sole using the numerically. Nonetheless, these problems have been studied to understand the local stress state of the seals under various static operating conditions leading to estimates of fatigue life. In addition, fluid pressure penetration analysis is typically performed by applying fluid opening pressure at the contact interface to study the likelihood of pressure leakage. In summary, static deformation of hyperplastic seals has been studied extensively. However, in addition to static loads the seals typically undergo fluctuating loads during operations. The impact of high frequency dynamic loads on the performance of elastomer seals is an area which needs further exploration and is the primary focus of this work.
In the current work, a computational framework is established to study the dynamic performance of elastomer seals using finite element method. The static material behavior of the seals is modeled using finite deformation theories and hyperplastic materials models. The frequency dependent response of the material is modeled by defining a viscoelastic model. This is achieved by defining a Prony series representation of the elastomer response. The solution to the structural problem follows the following steps – 1) resolve initial contact interpenetration to evaluate the preloads after seal installation, 2) apply static operational pressure loads and allow finite deformation of seals, 3) use the previous stress state as a preload and apply oscillating pressure loads (harmonic/random) at different frequencies using linear perturbation analysis. The performance of the seal is evaluated by estimating its fatigue life in response to the applied static and oscillating loads.
In addition to the structural analysis, thermal analysis of hyperelastic seals plays a key role in determining both the sealing behavior and life estimates of elastomer seals since these seals are often used for high temperature applications. Typically for the case of static loads, an approximation is made that the temperature distributions of the seal do not change as it undergoes deformation. In this case, a thermal solution can be predetermined and applied as a temperature condition for the subsequent structural analysis (1-way thermal structural coupling). However, for the case where the contacts undergo significant changes during deformation and/or due to viscoelastic heating (rise in temperature due to internal friction between polymer chains) of elastomer seals under dynamics loads, a fully coupled thermal-structural solution is needed. In this work, a fully coupled 2-way thermal-structural solution is developed for elastomer seals when subjected to both static and oscillating pressure loads. A comparison of both 1-way and 2-way thermal structural coupling results will be presented.
It is anticipated that this work will help understand the importance of studying dynamic behavior of elastomer seals. This work also provides a solution pathway for addressing the challenges associated with dynamic structural response of the seals and the associated thermal phenomenon – both of which affect the seal’s performance and life.