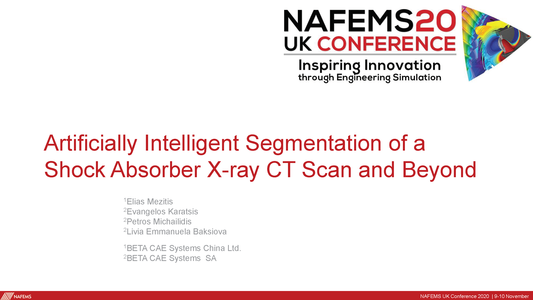
This presentation was held at the 2020 NAFEMS UK Conference "Inspiring Innovation through Engineering Simulation". The conference covered topics ranging from traditional FEA and CFD, to new and emerging areas including artificial intelligence, machine learning and EDA.
Resource AbstractAdvances in X-ray Computed Tomography (CT) have been remarkable during the last decade and have established the above technique not only in biomedical applications, but also in a broader range of other fields like engineering. From Cone-beam X-ray Computed Tomography (CBCT) scanners that are able of achieving resolution of the order of micrometres, for nano-structure inspections, to full vehicle scanners, x-ray Computed Tomography technology is present in most sectors of the automotive industry. It is rendered a suitable technique for product quality control, design evaluation and in general, a means of “digitising†an existing, real object of interest. In the Computer Aided Engineering (CAE) world, digitised real objects are ultimately converted into finite element models for realistic finite element simulations and fast product development. X-ray Computed Tomography provides a powerful, non-destructive method for achieving this even for complex multi-material assemblies. Limitations exist and are well known; however, emerging techniques and methods like machine learning can be proven valuable in the field of tomography post-processing allow for minimisation of uncertainty in material labelling and improvement of accuracy in segmentation.
In this work, a CT scan of a shock absorber is virtually disassembled with the aid of RETOMO utilising newly added artificial intelligent algorithms. The final resulting model is used to inspect the shock absorber anatomy and create a model for finite element studies. Innovative machine learning algorithms introduced in RETOMO greatly reduce required user time, while improving segmentation quality. The complete process from CT data to a suitable CAE model is demonstrated through a realistic reverse engineering scenario and facilitated through the use of RETOMO and ANSA, to ensure high-quality meshed model for consequent finite element simulations. Eventually the seamless interaction of the BETA suite is exemplified through the creation and setting up of a CAE model suitable for durability analysis.