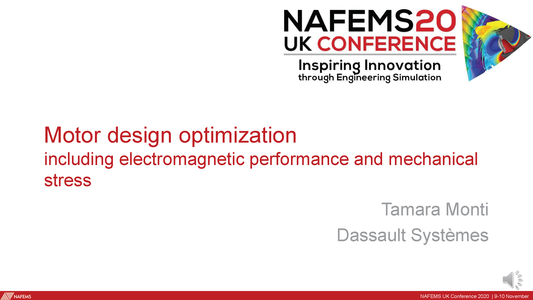
This presentation was held at the 2020 NAFEMS UK Conference "Inspiring Innovation through Engineering Simulation". The conference covered topics ranging from traditional FEA and CFD, to new and emerging areas including artificial intelligence, machine learning and EDA.
Resource AbstractThe challenges in designing drive units for vehicle traction applications are inherently multiphysical. In particular, the interplay between mechanical, thermal and electromagnetic requirements as well as lubrication and noise emission have to be taken into account.
Obvious goals for electrical machines used in electrical and hybrid vehicles are reasonable power, high power-to-weight ratio, good efficiency and low cost. However, numerous constraints, including mechanical stiffness, thermal and noise emission levels as well as a required durability, are limiting factors. Therefore, a design space exploration/optimization including proper constraints has to be performed to obtain a machine design fulfilling all requirements. Since the design space is typically quite large, performing all analyses in the individual domains for each parameter combination is not feasible due to the huge computational cost.
The proposed approach splits the optimization into successive phases. In the first phase the large design space is considerably reduced by an optimization including just a subset of the analyses with short execution times per design point. In the second phase the more time consuming analyses are performed on just a few “hot†candidates to investigate whether the residual constraints in the other domains are fulfilled. During the first phase the two dimensional motor geometry is optimized by performing both an electromagnetic steady-state analysis using sinusoidal currents and a mechanical stress analysis to check the design against mechanical stiffness constraints.
The electromagnetic analysis part consists of simulating (i) the behaviour over the operating range, (ii) loss and efficiency at selected operating points and (iii) demagnetization under worst-case fault condition.
The second optimization phase consists of loss and force calculation using inverter fed currents, which are transferred to subsequent thermal as well as noise and vibration calculations.
In case the requirements are not fulfilled, the design has to be adjusted either by improving the cooling system or improving the stiffness of the motor housing. If a viable solution is not found the electromagnetic design must be revisited, using tighter constraints for the optimization.
In order to seamlessly analyze the different aspects of the drive unit design, a parameterized model has been built using CATIA on the 3DEXPERIENCE platform. In this way the two dimensional FEM simulation models used in both the electromagnetic and in the mechanical domains, which require different levels of fidelity, are efficiently derived from one underlying parameterized 3D CAD geometry.
In this work an optimization of an interior permanent magnet synchronous machine (IPMSM) with 8 magnet poles, 48 slots, a distributed winding with 8 turns and NdFeB magnets has been performed.