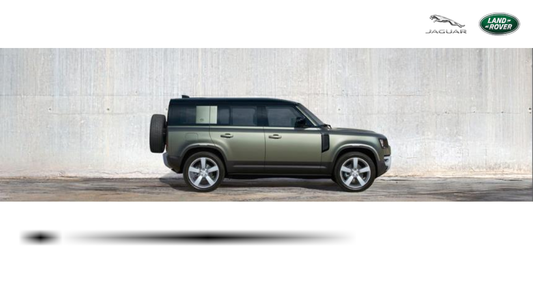
This presentation was made at the NAFEMS Seminar "Exploring Explicit Dynamics - Impact, Shock & Crash" held on the 13-14 April 2021.
Explicit Dynamics Finite Element Analysis has been used by industry and academia for many years. With advanced techniques such as particle methods, Arbitrary Lagrangian-Eulerian and advance failure methods becoming more prevalent in general purpose simulation packages, simulation engineers have never had such capabilities at their fingertips.
Modelling impact, shock & crash phenomenon is inherently difficult. The process is highly non-linear, materials are strain rate dependant, damage has to be realistically represented in order to capture the response of the product. The aim of this seminar was to present and discuss the challenges, and solutions in this field, using real engineering examples.
Resource AbstractWith increasingly challenging time and cost constraints being placed on vehicle development programmes, it is no longer feasible to conduct full-scale vehicle prototype testing before committing to significant investment in tooling and facilities. All development work is now carried out in the virtual domain, with vehicle testing performed for verification and homologation only, and failure to meet targets at this late stage can lead to extremely expensive rectification. At Jaguar Land Rover, one of the most demanding applications for CAE is high-speed crash, which involves many highly dynamic interacting systems, including active restraints components, and makes use of a wide range of tools and techniques. Most of the critical assessment criteria used in regulatory crash domains are based on crash dummy response values, and these dummies represent, in themselves, highly complex systems, comprising a large range of unique materials, connections, and mechanisms. Distinct characteristics of each dummy govern how they can best be used to help improve occupant crash protection, and a detailed knowledge of the structure and behaviour of each one is essential if the most effective restraint system is to be specified. High-fidelity CAE models of dummies are available, and, as well as providing accurate predictions of occupant injury values, they are invaluable in providing insights into behaviours that are not observable in a physical dummy. Since the 1950s, when the first attempts to create mechanical representations of humans were being undertaken in the US, the drive for increasing bio-fidelity has led to a continual development of new dummies. At the same time, the recognition that a restraint system designed to protect, for example, an average male might provide sub-optimal protection for occupants of different sizes has led to the development of a whole family of dummies, including smaller adults and children. These have all been reproduced in the virtual world, allowing the CAE engineer to construct models of any of the major crash modes currently in use. Alongside a progressive tightening of legal requirements, the advent of consumer test regimes such as the New Car Assessment Programme in North America and EuroNCAP in Europe has pushed automotive manufacturers to invest heavily in new component technologies improved CAE capabilities. These developments show no sign of abating, and radical changes in the way we will use vehicles in the future, including opportunities offered by autonomous vehicles, are already leading to new challenges, such as the possibility of new dummies that can adopt novel seating positions, and increasing use of human body models.
This paper will describe some aspects of the simulation of vehicle crash incorporating crash dummies, thereby illustrating the role of detailed dummy models in interpreting the crash results. Most importantly, the interactions between dummies and restraint components, which are fundamental to the loadings experienced by the dummies, and ultimately the injury values recorded, will be discussed. It will be shown that the increasing bio-fidelity of crash dummies brings its own difficulties in an engineering environment.
Pressure to deliver ever more sophisticated products, meeting increasingly stringent crash requirements, in as efficient a way as possible, means that the need for advanced simulation capabilities will continue to expand, and engineers will be challenged to push the state of the art forward, with the goal of increasing occupant safety. Recent Jaguar Land Rover vehicle launches, which all achieved the top 5* EuroNCAP rating, have shown the results that can be achieved through a consistent application of advanced virtual techniques.