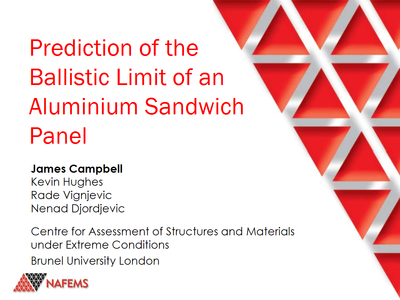
This presentation was made at the NAFEMS Seminar "Exploring Explicit Dynamics - Impact, Shock & Crash" held on the 13-14 April 2021.
Explicit Dynamics Finite Element Analysis has been used by industry and academia for many years. With advanced techniques such as particle methods, Arbitrary Lagrangian-Eulerian and advance failure methods becoming more prevalent in general purpose simulation packages, simulation engineers have never had such capabilities at their fingertips.
Modelling impact, shock & crash phenomenon is inherently difficult. The process is highly non-linear, materials are strain rate dependant, damage has to be realistically represented in order to capture the response of the product. The aim of this seminar was to present and discuss the challenges, and solutions in this field, using real engineering examples.
Resource AbstractOne concept for capture and deorbit of large items of space debris is the use of a harpoon to attach a cable to the debris. This requires good knowledge of the ballistic limit of the target structure as the harpoon must penetrate, but with a low residual velocity to limit further damage. We discuss the development of an explicit FE model for the prediction of the ballistic limit of an aluminium sandwich panel representative of a spacecraft structure. A detailed explicit finite element model of the panel was developed and results were compared with experimental data to investigate key modelling assumptions.
The model development followed a two stage process. In the first stage an initial model of the panel was developed to allow sensitivity studies to investigate modelling assumptions. This model was based on previous experience with modelling the ballistic limit of single aluminium plates. The sensitivity studies showed that the primary assumptions influencing the model behaviour were the strength and failure of the aluminium face sheets and the friction between projectile and panel. With the treatment of the experimental boundary conditions also important. In the second stage an updated model was used to investigate the ballistic limit of the panel and the influence of projectile shape and impact angle. The model results showed good agreement with experimental results for an ogive nose projectile, but overestimated the exit velocity for a flat nose projectile where the behaviour of the honeycomb core is a modelling challenge.
In this presentation we will discuss the model development process followed and the overall results achieved. We will cover in more detail the modelling of the panel face plates, discussing both the mesh density and material model. Mesh density required balancing required mesh resolution against overall computational cost. Several options for the face plate material model were investigated, from a simple strength model combined with a strain to failure criterion through to strain-rate effects and the use of a continuum damage mechanics model.