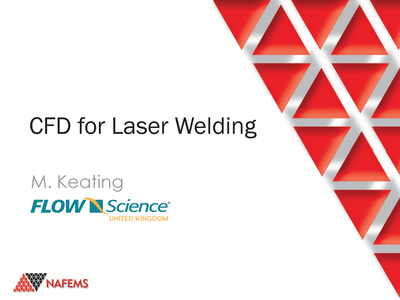
This presentation was made at the NAFEMS UK Seminar "Welding Simlation - How Much Validation is Enough?"
Resource AbstractTo meet stricter fuel economy standards in the automotive industry, automakers have increasingly turned to using aluminum diecast parts and panels due to their light weight and superior castability. Laser welding is a process by which die cast parts are connected to other semi-finished parts, such as profiles or tubes, through pressure-tight joints. However, gasses trapped during casting present challenges to the laser welding process and can cause additional defects such as porosity and melt pool blow-outs. Computational fluid dynamics (CFD) simulations of laser welding helps improve the process to achieve superior weldability. In this presentation, case studies on CFD simulations successfully employed to optimize process parameters such as welding speed, laser heat flux profiles, and angles of inclination to mitigate porosity formation are studied. Such CFD simulations serve as an initial, crucial step towards optimization of the process of laser welding of die-cast parts.
Such high-fidelity, multiphysics CFD models provide a framework to better understand laser welding and from the micro- and meso-scales and will be presented through a series of case studies.