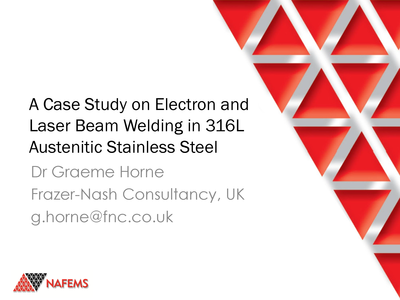
This presentation was made at the NAFEMS UK Seminar "Welding Simlation - How Much Validation is Enough?"
Resource AbstractWelding processes generate residual stresses and distortion within components and assemblies. The distortions can affect subsequent manufacturing processes, which reduces the quality of a component. They also generate further residual stress due to fit up and thermal contraction. Thus, residual stresses exist over both shorter length scales in the vicinity of the weld and longer length scales due to fit-up / shrinkage within the component or assembly. This work only considers the residual stresses directly resulting from the welding process and not the corresponding distortion. By definition residual stresses self-equilibrate within the system, so there will be regions within the system under compression and under tension. The residual stress state within a component is often a significant input to structural integrity assessments. The complex metallurgical effects resulting from welding frequently result in these regions being the focus of integrity assessments. Measuring the residual stress state within a material is not a trivial exercise, so predictions are usually relied upon when conducting integrity assessments. Weld residual stress predictions must be validated by measurement (preferably using more than one measurement technique) to provide confidence in their use. However, the quantity and quality of the validation will depend on the purpose and end use of the analysis.