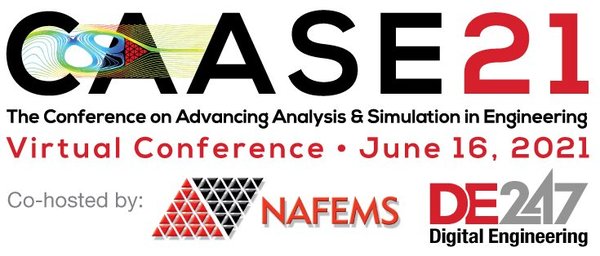
This presentation was made at the Conference on Advancing Analysis & Simulation in Engineering (CAASE21). This event was a collaboration between NAFEMS Americas and Digital Engineering (DE).
Resource AbstractThe Digital Engineering strategy of the Department of Defense, the drive to develop and use so-called digital twins, and several Certification by Analysis activities are driving the need for more simulation-driven design activities in the industrial base. This drive enables a shift of work from the physical environment into a virtual or digital environment, leading to significant decreases in the resources needed to design, produce, and keep aerospace assets operational.
To enable this strong reliance on engineering simulations, the full suite of systems engineering, robust design and stochastics methods and tools need to be employed during the simulation process. Accounting for variability and uncertainty that might occur during the manufacturing process and in the use of products is increasingly important for the assessment of component, sub-system and system performance with this simulation-driven design process. This talk will discuss the application of automated design and simulation processes, robust design techniques, probabilistic and stochastic methods for real-world design tasks in the area of advanced gas turbines. The talk will close with a discussion of the challenges in the area of simulation-driven design.
The key takeaways of this talk are that:
• Simulation-driven design can be applied to real world challenging problems.
• Accounting for variability and uncertainty is a key point in any simulation-driven design approach.
• Challenges still remain for a widespread application of simulation-driven design, especially in regulated industries.