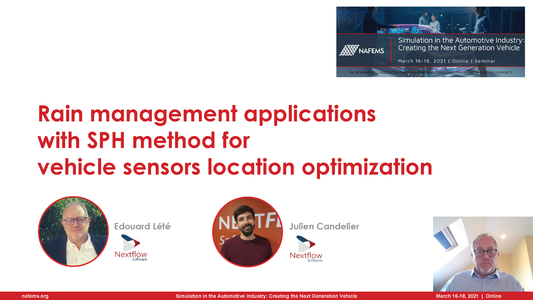
This presentation was made at the NAFEMS Americas Conference "Simulation in the Automotive Industry: Creating the Next Generation Vehicle" held on the 16-18 March 2021.
The automotive engineering community is now confronting the largest technology transformation since its inception. The demand to manufacture cleaner, safer, and smarter vehicles, along with providing an overall enhanced driving and ride experience, has never been higher. As a result, engineering teams must discover, evaluate, and successfully implement leading-edge technology and methods to produce reliable, effective results.
Hence, the challenges for automotive engineers are enormous and require a significant increase in the upfront use of numerical simulation capabilities, methods, and processes such that they’re able to efficiently design, manufacture and deliver these innovative technologies to market in greater speeds than ever before.
Resource AbstractNumerical simulation software based on the Smoothed Particle Hydrodynamics method (SPH) is solving the Navier-Stokes equations with a Lagrangian formulation that extends the reach of Computational Fluid Dynamics (CFD) to new domains.
Meshing-free is the main characteristic of the SPH method. Fluid is described by particles which interact with each other. Thereby, engineers can spend time on physics and not on complex meshing. This key advantage opens the door to democratization, as the product is easy to learn and does not require meshing expertise. The setup of a new analysis can also be finalized in few hours (instead of days or weeks) even with complex geometries and/or highly dynamics phenomena, such as rain management applications.
Sensors in ADAS and autonomous vehicles have increasingly been used since few years. Camera sensors are extremely sensitive to soiling, as they are located on external part of the vehicle and interact with environmental sources of soiling, such as rain drops, dust, mud. Rain management is also crucial when dealing with driver side mirror view.
In this paper, we will review several rain management applications, using key capabilities for treatment of surface tension and aerodynamic forcing, starting with an orphan mesh obtained from a 3D scan and an external aerodynamic flow, previously computed by a traditional CFD code.
The starting point is the reuse of the aerodynamic field obtained for car performance study and to add some value to this almost mandatory simulation. The aerodynamic simulation can be obtained from any software/method: Finite Volume Method, Lattice-Boltzmann Method. We have developed an aerodynamic forcing algorithm that allows to deal only with the liquid phase during the simulation and consider the influence of air which is crucial at some driving speed. Considering that SPH method is very versatile when considering boundary motion, we can easily model wiper motion and driver visibility or even study soiling from wheel spray (see figure 1). Engineers can also consider multiscale analysis using local refinement of fluid particles (Chiron et al. (2018)).
An additional non-Newtonian model can be used to simulate mud projection on cameras, as well with aerodynamic forcing. The surface tension model can predict the behavior of the mud with different surface treatment and allows optimization of sensor location.
Without changing CFD specialists’ favorite software and with just little training, we can study advanced challenges in water and liquid simulation. Furthermore, starting from an orphan mesh and not necessarily from a CAD surface, it opens the simulation to new horizons in life sciences or nature, where there is no CAD model to be used.