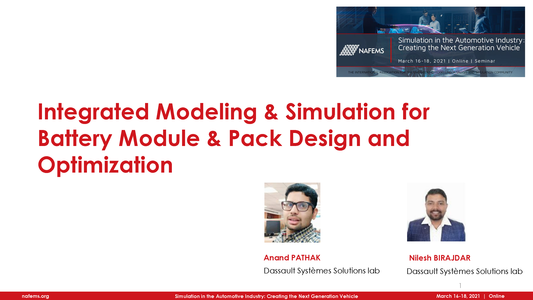
This presentation was made at the NAFEMS Americas Conference "Simulation in the Automotive Industry: Creating the Next Generation Vehicle" held on the 16-18 March 2021.
The automotive engineering community is now confronting the largest technology transformation since its inception. The demand to manufacture cleaner, safer, and smarter vehicles, along with providing an overall enhanced driving and ride experience, has never been higher. As a result, engineering teams must discover, evaluate, and successfully implement leading-edge technology and methods to produce reliable, effective results.
Hence, the challenges for automotive engineers are enormous and require a significant increase in the upfront use of numerical simulation capabilities, methods, and processes such that they’re able to efficiently design, manufacture and deliver these innovative technologies to market in greater speeds than ever before.
Resource AbstractAccelerated vehicle electrification with enhanced shift towards renewable energy has potential to tackle CO2 emission problem and slow down climate change. Automotive industry is undergoing immense transformation to meet the current electrification trend and realize this potential. Consumers have high expectations from the new Electric Vehicles for range, speed and safety. Battery pack - the new fuel tank in a car- is the most vital component to meet these expectations.
In order to develop a battery pack that meets these demands of future mobility,
- OEM’s need to streamline their engineering processes.
- The battery pack which contributes to nearly half the cost of the vehicle needs to be compact, lightweight, and well protected from thermal or mechanical safety issues.
- Companies also need to modularize these packs to best suit all classes and variants.
- Knowing that 90% of decisions are made during concept phase, it is critical to evaluate all the architecture choices of a battery pack. With the current complex and disconnected legacy tools, OEM’s are severely limited in the number of concept architectures they can study.
To address these challenges, a systems engineering approach combining requirements management, 1-D simulation, parametric 3D modeling, and tightly integrated 3D simulation is used. Combining these approaches accelerates the rate of design iteration and leads to better designs in less time. Firstly, a 1D system is developed to quantify the battery pack performance such as range, max acceleration and max temperature during a drive-cycle. A trade-off is then performed between the cylindrical and pouch cells to meet the battery performance requirements. These system level studies help to finalize the cell form factor and the components of the battery pack architecture. Following-up, a parametric concept model of a battery pack frame is built. The topology, cross sections and layout of structural members of this model is varied to optimize NVH and crashworthiness performance. The detailed battery pack is then built with parametric modules arranged in the optimized frame based on concept study. Finally, this detailed battery pack architecture is validated for crashworthiness and thermal performance.
By using CATIA and SIMULA apps on the 3DEXPERIENCE Platform, this battery development process was executed with faster ideation, concept creation, detailed design and validation. Additionally, the integration of all necessary tools into a single user experience reduces time spent on process development and enables quick replication. A case study illustrates these results.