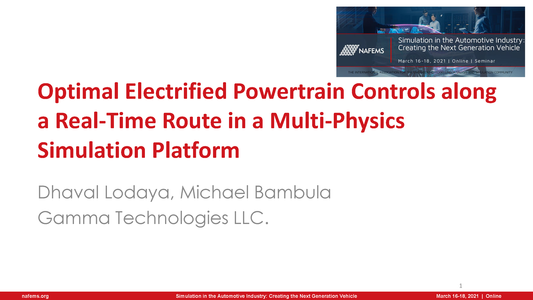
This presentation was made at the NAFEMS Americas Conference "Simulation in the Automotive Industry: Creating the Next Generation Vehicle" held on the 16-18 March 2021.
The automotive engineering community is now confronting the largest technology transformation since its inception. The demand to manufacture cleaner, safer, and smarter vehicles, along with providing an overall enhanced driving and ride experience, has never been higher. As a result, engineering teams must discover, evaluate, and successfully implement leading-edge technology and methods to produce reliable, effective results.
Hence, the challenges for automotive engineers are enormous and require a significant increase in the upfront use of numerical simulation capabilities, methods, and processes such that they’re able to efficiently design, manufacture and deliver these innovative technologies to market in greater speeds than ever before.
Resource AbstractIn recent years, electrification of vehicle powertrains has become more mainstream to meet regulatory fuel economy and emissions requirements. Amongst the many challenges involved with powertrain electrification, developing supervisory controls and energy management of hybrid electric vehicle powertrains involves significant challenges due to multiple power sources involved. Optimizing energy management for a hybrid electric vehicle largely involves two sets of tasks: component level or low-level control task and supervisory level or high-level control task.
In addition to complexity within powertrain controls, advanced driver assistance systems and the associated chassis controls are also continuing to become more complex. However, opportunities exist to optimize energy management when a cohesive interaction between chassis and powertrain controls can be realized. To optimize energy management along a given route, certain information such as the projected vehicle route, driver behavior, and battery charge level should be considered.
In this case study, simulation models of a parallel P0P4 hybrid electric vehicle are presented, which optimize powertrain controls using the Dynamic Programming approach. This virtual vehicle model is exercised through HWFET and FTP-75 regulatory driving cycles to establish a performance baseline in a controlled driving environment. For comparison to off-cycle driving, the virtual vehicle is then also exercised through a real-world driving scenario over real-world roads, with similar trip characteristics to the regulatory tests, but with real traffic conditions during the day. This comparison provides insights into how optimized real-world fuel economy results can differ compared to the controlled testing environment, and how predictive powertrain controls can offer “in-situ” optimization of energy management.