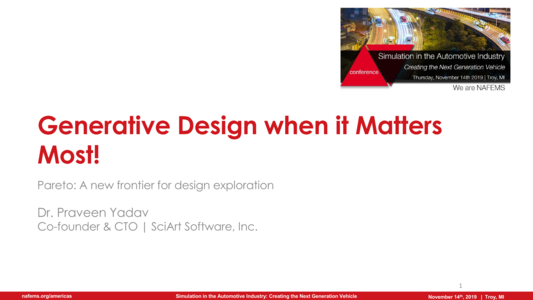
This presentation was made at the NAFEMS Americas "Creating the Next Generation Vehicle" held on the 14th of November in Troy.
The automotive engineering community is now confronting the largest technology transformation since its inception. This includes the electrification of powertrains for more efficient consumption and cleaner emissions, the reinvention of the battery with fast wireless charging capabilities and finally the advent of a fully autonomous vehicle. Compounding to these technology changes, the automotive companies design verification process is moving away from a major reliance on physical testing to almost a full virtual simulation product verification process.
The automotive engineering community is now confronting the largest technology transformation since its inception. This includes the electrification of powertrains for more efficient consumption and cleaner emissions, the reinvention of the battery with fast wireless charging capabilities and finally the advent of a fully autonomous vehicle. Compounding to these technology changes, the automotive companies design verification process is moving away from a major reliance on physical testing to almost a full virtual simulation product verification process.
Resource AbstractNext generation vehicles require lighter and better‐performing designs. Given a structural problem, the challenge engineers face is to determine where and how to distribute the material to optimize the topology. Finite element analysis (FEA) is a commonly used tool; however, FEA can only provide hints on where the engineer should remove material. The actual process of carefully removing material can be arduous and error prone. There is no guarantee that the final design generated through this trial‐and‐error process is even close to optimal. Topology optimization is a powerful automated process for performance‐constrained weight reduction. It relies heavily on FEA, but it automates the process of material removal, resulting in a highly optimized design. Topology optimization, one of the tools in generative design, provides rapid solutions to design problems, shaving weeks off product development cycles. There are several topology optimization methods and software implementations, but all of them rely on FEA and optimization techniques. However, they differ on the specific FEA method, the optimization technique, the number of design iterations required, ease‐of‐use, constraint handling, multi‐load and multi‐physics capabilities, etc.
Further, there is a lot of excitement today in additive manufacturing; one can fabricate parts in virtually any shape. This offers several advantages over traditional manufacturing and has the potential to revolutionize the way things are manufactured. Topology optimization directly caters to 3D printing because the output from topology optimization is typically an STL file, that can be directly 3D printed, and for most 3D printing processes (especially, metal 3D printing), material reduction is critical. Through topology optimization, one can dramatically reduce the amount of material used in a design.
No technology is perfect, and not all designs are feasible; therefore, strength/weakness analysis is necessary to maximize the utility of generative design. Strength and weaknesses information can be collated into a Pareto frontier; the boundary of feasible and infeasible designs, and exploring the Pareto frontier allows engineers to understand the trade-offs and maintain a digital thread that is quantitatively richer in information, managing requirements to design and validated parts as a simulation lifecycle management.
Finally making the tools easy to use allows design engineers to create the digital thread quickly and efficiently. This is the critical step towards democratizing simulation analysis, and thus providing generative design when it matters most!