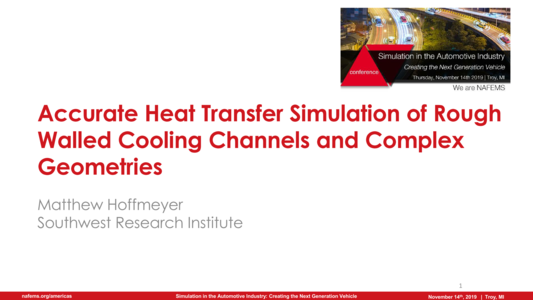
This presentation was made at the NAFEMS Americas "Creating the Next Generation Vehicle" held on the 14th of November in Troy.
The automotive engineering community is now confronting the largest technology transformation since its inception. This includes the electrification of powertrains for more efficient consumption and cleaner emissions, the reinvention of the battery with fast wireless charging capabilities and finally the advent of a fully autonomous vehicle. Compounding to these technology changes, the automotive companies design verification process is moving away from a major reliance on physical testing to almost a full virtual simulation product verification process.
The automotive engineering community is now confronting the largest technology transformation since its inception. This includes the electrification of powertrains for more efficient consumption and cleaner emissions, the reinvention of the battery with fast wireless charging capabilities and finally the advent of a fully autonomous vehicle. Compounding to these technology changes, the automotive companies design verification process is moving away from a major reliance on physical testing to almost a full virtual simulation product verification process.
Resource AbstractAs regulations continue to drive efficiency improvements in Internal Combustion Engines and the mobility industry continues to electrify and hybridize, multiple strategies are being used to increase powertrain efficiency. One possible target for increased efficiency is within the cooling system. For internal combustion engines, advanced combustion strategies continue to push metal temperatures and stresses to their limits. In electric vehicles, battery cells must be maintained within a narrow operating temperature range in order to maximize battery life and performance. In both systems, active cooling is essential but also creates a parasitic energy drain in the form of pumping losses. In addition, too much cooling in internal combustion engines decreases combustion efficiency. Southwest Research Institute launched a project last year to investigate how complex internal geometries, made possible by additive manufacturing, could be used to enhance heat transfer. The study examined cooling in both the forced convection and nucleate boiling regimes. This presentation briefly highlights the results of that study, but primarily covers how simulation was used to understand how the additively manufactured geometries were enhancing heat transfer from the wall into the coolant. Multiple modeling techniques on the fluid side were evaluated. The detailed modeling evaluation included grid sensitivity studies, rough surface wall treatment formulations, and turbulence models. The end goal was to develop a method that could accurately model the heat transfer enhancement but be efficient enough to scale up to a full size cooling system analysis. This project revealed that accurate cooling heat transfer models need to correctly account for wall roughness while also characterizing the complex turbulent flow dynamics generated by the complex geometric features made possible by additive manufacturing. This project demonstrates that it is possible to accurately model those complex features, but it is also very easy to underestimate the benefits provided by complex geometries if the model isn’t set up appropriately. Several best practices were established to use in future cooling system analyses. The ability to accurately model full systems that incorporate these new geometries will lead to optimized designs that can target cooling in specific zones of a structure. These optimized designs will be able to limit peak system temperatures with lower coolant flow rates which will reduce pumping losses, thereby resulting in more efficient powertrain designs.