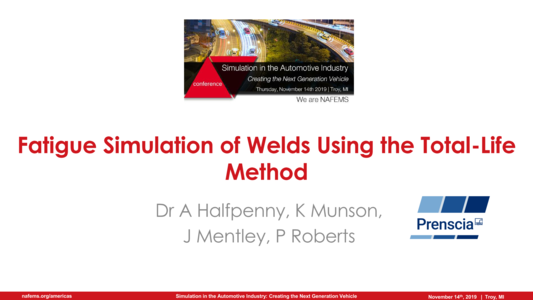
This presentation was made at the NAFEMS Americas "Creating the Next Generation Vehicle" held on the 14th of November in Troy.
The automotive engineering community is now confronting the largest technology transformation since its inception. This includes the electrification of powertrains for more efficient consumption and cleaner emissions, the reinvention of the battery with fast wireless charging capabilities and finally the advent of a fully autonomous vehicle. Compounding to these technology changes, the automotive companies design verification process is moving away from a major reliance on physical testing to almost a full virtual simulation product verification process.
The automotive engineering community is now confronting the largest technology transformation since its inception. This includes the electrification of powertrains for more efficient consumption and cleaner emissions, the reinvention of the battery with fast wireless charging capabilities and finally the advent of a fully autonomous vehicle. Compounding to these technology changes, the automotive companies design verification process is moving away from a major reliance on physical testing to almost a full virtual simulation product verification process.
Resource AbstractWelding is often necessary in product design and production, but it can lead to susceptibility to fatigue cracking. Predicting the fatigue life of welded components is therefore critical to ensuring product durability requirements are met.
A number of analytical approaches have been used predict to weld durability. These existing methods may struggle to accurately predict fatigue life in some cases. This is particularly true in cases of complicated weldments and advanced materials that have become more prevalent in the current lightweighting environment. In some weldments, cracks may initiate but grow very slowly – or not at all – depending on how the weld is designed. Understanding the total life of the weld becomes very important to ensuring product durability.
The total-life fatigue method addresses this analysis gap, bringing powerful new analysis capabilities for a more accurate prediction of weld fatigue life that results in improved product durability, reduced overdesign, and lower weight and cost. Total-life uses an integrated approach to model fatigue over the entire lifetime of the component – from very early stages of crack initiation to macroscopic crack growth and final fraction – to give a more accurate determination of weld life. This combined approach of crack initiation and crack growth overcomes limitations and assumptions that are inherent in adopting either of these approaches separately.
This paper describes a finite element-based (FE) methodology for implementing this whole life fatigue analysis in a CAE environment. This new method offers numerous benefits over traditional weld fatigue analysis techniques, such as recognizing fatigue life as being dependent on both crack initiation and crack growth; the use of fracture mechanics-based crack growth and crack tip plasticity modelling; insensitivity to initial crack length assumptions; incorporating the influence of weld geometry and residual stress on life; the use of lightweight FE modelling techniques; and the ability to include complicated multiaxial loading. This paper describes how this total-life method has been implemented in a software solution, including descriptions of the required inputs for FE modelling, material properties, residual stresses, and applied loading.