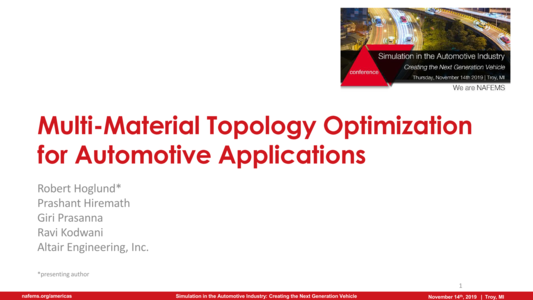
This presentation was made at the NAFEMS Americas "Creating the Next Generation Vehicle" held on the 14th of November in Troy.
The automotive engineering community is now confronting the largest technology transformation since its inception. This includes the electrification of powertrains for more efficient consumption and cleaner emissions, the reinvention of the battery with fast wireless charging capabilities and finally the advent of a fully autonomous vehicle. Compounding to these technology changes, the automotive companies design verification process is moving away from a major reliance on physical testing to almost a full virtual simulation product verification process.
The automotive engineering community is now confronting the largest technology transformation since its inception. This includes the electrification of powertrains for more efficient consumption and cleaner emissions, the reinvention of the battery with fast wireless charging capabilities and finally the advent of a fully autonomous vehicle. Compounding to these technology changes, the automotive companies design verification process is moving away from a major reliance on physical testing to almost a full virtual simulation product verification process.
Resource AbstractTopology optimization has become an integrated part of the design cycle where light-weighting and robustness are important for vehicle systems. With advances in novel manufacturing methods, it has become easier to manufacture parts and assemblies with multiple materials, like over-molds of plastic and metal, steel-aluminum frames, etc. Multi-material optimization can provide the benefits of achieving feasible designs in limited design regions, light-weighting by selecting materials more efficiently, and cost savings at manufacturing volumes for automotive applications.
In this paper, a practical methodology for multi-material topology optimization is presented with examples to determine the optimal load-paths for structural components considering multiple materials. An available “package space” is considered as in a standard topology optimization, where material can be kept or removed. Models are constrained at mounting locations and loading is applied at attachment points, as in a typical analysis setup. Next, topology optimization is performed with different objectives and constraints, e.g. to minimize mass and minimize the effective cost with constraints on displacements, and various concepts are generated based on multiple material models that are considered in the design space.
By formulating the problem in this manner with multi-material optimization, trade-offs between the materials can be evaluated, i.e. the stiffness of steel vs. the mass savings of aluminum, and the potential difference in material costs. Including a cost function within the structural optimization to relate relative expense of different materials can take the consideration of production costs into the optimization problem.
The results of the multi-material optimization workflow are presented and summarized with recommendations for common design scenarios. Inclusion of all relevant constraints is important to formulate and drive the optimization approach correctly. The multi-material topology optimization method can be utilized to determine optimal material placement with a structure from a list of available options, and balance the trade-offs between materials with different weight, stiffness, and raw material cost in a concept-level topology optimization.